The Best Strategy To Use For Alcast Company
The Best Strategy To Use For Alcast Company
Blog Article
The Only Guide to Alcast Company
Table of ContentsAlcast Company - An OverviewGet This Report about Alcast CompanyAlcast Company - An OverviewThe Best Strategy To Use For Alcast CompanyThe Only Guide to Alcast CompanyThe Definitive Guide for Alcast Company
The refined difference hinges on the chemical material. Chemical Comparison of Cast Light weight aluminum Alloys Silicon advertises castability by minimizing the alloy's melting temperature and boosting fluidness throughout casting. It plays an important role in allowing intricate molds to be loaded precisely. In addition, silicon contributes to the alloy's stamina and put on resistance, making it useful in applications where toughness is vital, such as auto parts and engine parts.It likewise boosts the machinability of the alloy, making it less complicated to refine into completed products. In this way, iron contributes to the general workability of aluminum alloys.
Manganese adds to the strength of light weight aluminum alloys and enhances workability. Magnesium is a lightweight component that provides strength and effect resistance to aluminum alloys.
Alcast Company - An Overview
Zinc boosts the castability of light weight aluminum alloys and helps control the solidification process throughout spreading. It boosts the alloy's stamina and firmness.

The primary thermal conductivity, tensile strength, return strength, and elongation differ. Amongst the above alloys, A356 has the highest thermal conductivity, and A380 and ADC12 have the least expensive.
The Single Strategy To Use For Alcast Company
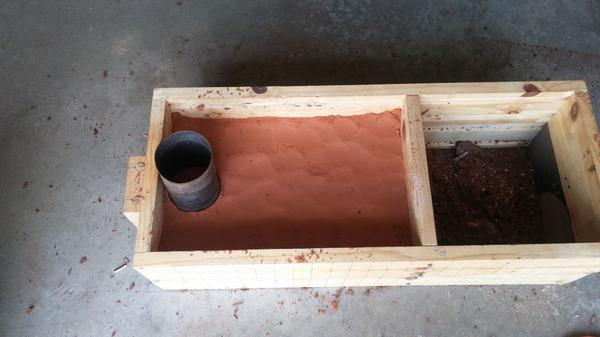
In accuracy casting, 6063 is appropriate for applications where detailed geometries and premium surface area finishes are vital. Instances include telecommunication enclosures, where the alloy's remarkable formability enables sleek and visually pleasing layouts while preserving architectural stability. Likewise, in the Lighting Solutions market, precision-cast 6063 components create elegant and effective illumination components that call for elaborate forms and great thermal performance.
The A360 exhibits superior elongation, making it ideal for facility and thin-walled components. In precision spreading applications, A360 is well-suited for industries such as Customer Electronic Devices, Telecommunication, and Power Devices.
Some Known Details About Alcast Company
Its distinct residential or commercial properties make A360 a useful selection for accuracy spreading in these sectors, enhancing product longevity and top quality. aluminum casting manufacturer. Light weight aluminum alloy 380, or A380, is a widely utilized spreading alloy with numerous distinct characteristics.
In precision spreading, light weight aluminum 413 beams in the Customer Electronics and Power Tools markets. It's commonly utilized to craft detailed components like mobile phone real estates, electronic camera bodies, and power device casings. Its accuracy is remarkable, with limited resistances as much as 0.01 mm, making certain flawless item setting up. This alloy's exceptional rust resistance makes it an exceptional option for outdoor applications, making sure resilient, resilient discover here items in the stated sectors.
Alcast Company Things To Know Before You Get This
The aluminum alloy you choose will considerably impact both the casting process and the homes of the final item. Since of this, you have to make your decision meticulously and take an informed approach.
Figuring out one of the most ideal aluminum alloy for your application will certainly indicate considering a vast selection of attributes. These comparative alloy attributes comply with the North American Pass Away Spreading Organization's standards, and we've divided them right into two categories. The very first group addresses alloy qualities that influence the manufacturing process. The second covers attributes impacting the residential or commercial properties of the final item.
The Facts About Alcast Company Uncovered
The alloy you choose for die spreading straight impacts several facets of the casting procedure, like just how simple the alloy is to work with and if it is susceptible to casting defects. Hot cracking, likewise called solidification breaking, is a common die casting issue for light weight aluminum alloys that can lead to internal or surface-level splits or splits.
Specific aluminum alloys are extra susceptible to hot cracking than others, and your option should consider this. It can damage both the cast and the die, so you ought to look for alloys with high anti-soldering homes.
Deterioration resistance, which is currently a remarkable feature of aluminum, can vary considerably from alloy to alloy and is a vital characteristic to take into consideration depending on the environmental conditions your product will be revealed to (Aluminum Castings). Use resistance is an additional building typically sought in aluminum items and can separate some alloys
Report this page